The Role of Inkjet Technologies in Additive Manufacturing
- Jun 3, 2020
- 5 min read
Author: George Gibson, President, G2 Tech Acceleration, Fairpoint, New York
We’ve been given a glimpse of the future of manufacturing and additive manufacturing (AM) plays a big role. The manufacturing sector is huge, globally about $12T. Right now, Deloitte Global predicts AM will garner sales from large public companies alone, of over $3B in 2020. Not small by any means but with lots of headroom for growth.
Before we get too far, let’s define out terms. AM derives its name because the objects that it produces are built up layer by layer, unlike traditional subtractive techniques where you start with a block of material and remove some to form the object. Many people equate AM with 3D printing. And while all 3D printing is AM, not all AM is 3D in the conventional sense. AM includes things like printed electronics and functional printing. In these cases, the structures produced are indeed the superposition of layers, but the total object height might be less than 50 microns. At the recent IMI Inkjet Conference 2020, one speaker referred to these applications as 2.5D.
There are a large number of techniques that are employed for AM but they generally fit into one of 7 categories:
· Vat polymerization
· Material extrusion
· Material jetting
· Binder jetting
· Powder bed fusion
· Direct energy deposition
· Sheet lamination
A number of these employ inkjet technologies as a critical process step.
The first thing to say is that much of the intuition you have developed about inkjetting in 2D still is useful in AM. Control of ink rheology and surface tension remains important. Tuning heads and materials for each other and careful manipulation of jetting parameters (frequency, waveform, …) also remain important. But generally, the materials you will use have different characteristics. Jetting biologics for tissue scaffolds, or jetting cell suspensions for instance, do provide some unique challenges.
Direct material jetting is the most straightforward of inkjet-based techniques. As the name implies, these techniques directly jet the material composing the part. In some embodiments waxes or photopolymers which harden on cooling or exposure to UV light are used. These approaches lend themselves to multi-material printing. Multi-material processes are particularly important if the objects you are constructing require support materials to improve geometric fidelity or if color is important. One recent example of this type of system is the Stratasys Objet260 Connex3. A great YouTube video of that device in operation can be found here. Beyond simply polymers, material jetting approaches can be used with a number of different materials including ceramics, drugs, and biologicals, albeit presenting significant new technology. Printed electronics, a major application area for material jetting, where you might jet a conductive ink or a dielectric material onto a substrate, similarly poses a number of unique challenges.
Another inkjet dependent AM technique is binder jetting. There are a large number of variants of this approach which share some fundamental characteristics. They meter a fine layer of powdered material on the build platform, jet some material on the powder, sometime apply some energy source, meter a second powder layer and repeat. These devices do not need to use support structures, as the unaffected powder provides support for the growing object. Frequently the powder beds are run at elevated temperature. Careful control of temperature uniformity during the build and of the cooling ramp are often required to minimize the effects of stresses accumulated during the build cycle, which may warp finished parts or cause other unacceptable geometric deviations. Full color is achievable in many embodiments. Often the objects produced are porous and require post processing to become air or fluid tight. Some great examples of this approach include offerings from ExOne, Voxeljet, and Hewlett Packard’s Multijet Fusion.
A novel approach to inkjet-based 3D printing is called Composite Based Additive Manufacturing (CBAM). Developed by Impossible Objects it employs sheets of non-woven fabrics of carbon, glass, Kevlar, polyester or other fibers. Each sheet becomes an image plane of the object to be printed. The image data is jetted onto the sheets and the sheets are then blanket-dusted with a polymer. Air is used to remove the polymer for the non-image area and the sheets compiled. When the entire object has been printed, the accumulated sheets are consolidated using heat and pressure. The unimaged portions of the sheet can be removed with media blasting. An animation of this process can be found here. A wide variety of polymers can be used from more common materials including polyolefins, nylons, elastomers to performance polymers including PEEK. Composite objects are, of course, of particular interest in a number of important markets including the automotive and aerospace sectors where their superior strength to weight ratio and thermal deflection properties are of particular importance.
Apparently appearing first in Danish in 1948, ‘it is difficult to make predictions, especially about the future,’ remains an important touchstone. That said, here are some vectors that are likely to shape the industry over the next few years. Technology innovation will remain important. You need only count the number of patents issued each month to get a sense of the rate of advancement. While inkjet itself may be maturing, its application to AM is still evolving rapidly. It is quite clear that the rate of new firm formation in AM remains robust. This is reflected in the amount of venture funding devoted to the area. Similarly, mergers and acquisitions play an increasing role both among the larger AM companies and between large AM users and advanced technology start-ups. The diversity of applications will continue to increase, spurred on by the increasing speed of printer speed, size of build volume, and range of usable materials. Additionally, as AM turns the corner from being largely used for rapid prototyping to a manufacturing capable technique, we will see increasing emphasis on quality tools and metrology, automation (especially of post processing), and workflow management systems.
G2 Tech Acceleration will begin offering a bimonthly Additive Manufacturing Industry Gazette in the near future. The Gazette contains coverage to help you stay abreast of the most recent of developments in the sector without having to spend hours compiling it yourself. The publication, to be published 6 times a year, contains sections on:
· Industry news
· Financial transactions shaping the sector
· Academic papers and presentations
· Patents
· Editorial content
It will be available by subscription and selected 2019 issues will be available for free. Look for the announcement at https://g2dvdt.com/.
About the Author
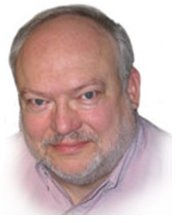
Author: George Gibson, President, G2 Tech Acceleration, Fairport, New York
After working many years for Xerox, AM Graphics and, Savin Corporation, George founded G2 Tech Acceleration, a technology maturation, commercialization, and strategy consultancy in 2019. Based in Fairport, NY; G2 Tech Acceleration offers bespoke training and hands-on assistance focusing on achieving benchmark breaking time to commercialization. His customers include start-ups, mid-sized firms, and Fortune 500 companies.
His technology foci include 2- and 3- (and sometimes 4-) dimensional printing, printed electronics, intelligent packaging, print to shape, printed sensors and IoT enabled sensor networks, and blockchain.
George earned his undergraduate and graduate degrees in Chemistry from Binghamton University and holds an MBA from the University of Rochester’s Simon School and is a certified Lean Six Sigma Black Belt. He has published over 20 papers in the academic and trade press, is inventor or co-inventor of 72 US patents and is a frequent lecturer on printing technologies, technology strategy, process management, decision making and portfolio management.
Comments